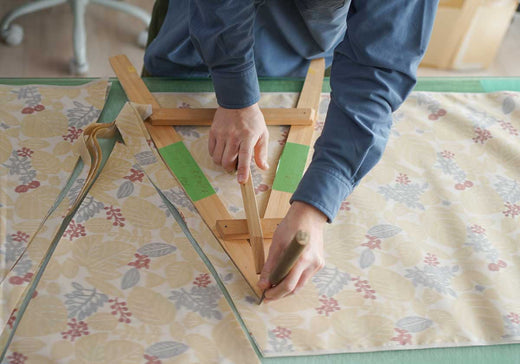
Japanese umbrellas

The History and Unique Characteristics
JAPAN-MADE
WESTERN
UMBRELLAS
Western-style umbrellas were introduced to Japan in the late Edo period and refined through Japanese craftsmanship and a unique sense of aesthetics. We will introduce the charm of these Japanese-made Western umbrellas, which carry on that tradition and remain alive today.
The Beginning of Umbrellas and Japan-Made Western Umbrellas
The Origin of Umbrellas
It is said that the origin of umbrellas goes back to around the 6th century BC in ancient Egypt. Sculptures and paintings remain depicting attendants holding an umbrella over the head of a king, where umbrellas were used as a symbol of authority, mainly for shade. By around 400 BC, “parasols” had become common among women in Greece.
Fast-forward in time to the 1660s, when umbrellas spread to France, then Italy and Spain, becoming a fashionable item for upper-class women. In London around 1750, it is said that Jonas Hanway’s use of a rain umbrella was a major turning point. After that, umbrellas became essential for keeping out the rain and a must-have for English gentlemen.

A parasol from 1868 (the first year of the Meiji era) by “Senjokou Sakamoto Shoten.” (Related article)

A parasol believed to have been made in the late Meiji era (owned by Komiya Shoten). (Related article)
Wagasa (Traditional Japanese Umbrellas) and Western Umbrellas
It is said that Western umbrellas first came to Japan in 1854 with the arrival of Commodore Perry(The US navy officer). Records mention that “they looked black in color, resembling a bat,” which is how they came to be called “koumouri-gasa” (bat umbrellas).
During the lively era of the Meiji Restoration, Western umbrellas were imported as luxury goods owned only by members of the upper class. A major role in this was played by Sakamoto Shoten, who had been manufacturing and selling the popular Edo-period face powder called “Senjokou.” Its fifth-generation owner, Tomohisa Sakamoto, began importing and selling Western umbrellas and parasols, earning a reputation as a pioneer of Western umbrellas in Japan. Later, the sixth-generation owner, Tomoshichi Sakamoto, traveled to Europe to learn the manufacturing process of Western umbrellas and parasols. He spent five years accomplishing the first domestic mass production in Japan.
Decline of Japan-Made Western Umbrellas After the Period of Rapid Economic Growth
During Japan’s period of rapid economic growth, there were more than 70 umbrella-related workshops just in Tokyo’s old downtown area, where Komiya Shoten is located, and a large number of umbrella artisans worked there, making it a thriving industry. However, by the Heisei era (1989–2019), many companies in the umbrella industry moved their main manufacturing to Asian countries. As a result, most Japanese umbrella artisans went out of business, and many umbrella shops went bankrupt. Today, only a few shops in Tokyo continue to make Japanese-made umbrellas.
Rokumei Ombrelle
In 2019, Komiya Shoten completed a replica model inspired by an original from Senjokou Sakamoto Shoten. We delved into historical documents to reproduce everything we could, from design and shape to size. This replica model is called the “Rokumei Ombrelle” and is on display and for sale at Komiya Shoten in Higashi-Nihonbashi.
Rokumei Ombrelle, a Parasol Recreated from the Meiji Era

The Tradition of Fabric Making
Koshu-ori
One of the biggest attractions of Japanese-made Western umbrellas is that they use “Koshu-ori,” a traditional weave from Yamanashi Prefecture with over 400 years of history. Drawing on the vibrant pre-dyed threads colored by the spring water of Mt. Fuji, we showcase the allure of this lustrous woven fabric.
The Roots of Koshu-ori and Over 400 Years of Weaving Culture
Koshu-ori is a textile with a history of more than 400 years, produced in the Gunai region around Fujiyoshida City in Yamanashi Prefecture. Its origins can be traced to a pure silk fabric called Kaiki. The tradition of weaving in the Gunai region itself goes back about 1,000 years to the Heian period. According to records in the Engishiki—a collection of laws and regulations from that time—textiles from this area were paid as tribute. The specific origin of Kaiki is thought to be around 400 years old, developed from fabrics introduced to Japan through the so-called Nanban trade (Portuguese and Spanish trade). Among the imported textiles and threads were items known as “kaiki,” which provided the basis for the Kaiki produced in Japan. During the Edo period, Yasutomo Akimoto, the first lord of the Gunai region, brought in weaving experts from his hometown in Joshu to develop the local industry. By the Genroku era (1688–1704), Kaiki had become widely known as a high-end textile.

“Hogushi-ori,” where the weft threads are removed from a temporary weave and carefully unraveled by hand as it’s woven

A double-sided fabric woven with a shuttle loom
Beautiful Luster from Pre-Dyeing
One of the traditional techniques passed down in this region is “pre-dyeing,” where threads are dyed before they are woven, resulting in bright, lustrous threads. A key part of the pre-dyeing process is the water used for dyeing—the cleaner the water, the better the color turns out. Thanks to the spring water of Mt. Fuji, which emerges after passing through lava layers over a long period, the threads are dyed deep and vibrant. Then, using yarn finer than a strand of hair, the fabric is woven with high density and delicate precision.
Our Passion for ‘Narrow-Width’ Fabric
Generally, there are two types of fabric widths: “wide-width” and “narrow-width.” Wide-width fabrics are about 120–130 cm in width, whereas narrow-width fabrics are about 60 cm and are particularly suited for umbrellas. The narrow-width fabric is typically woven on a “shuttle loom.” A device called a shuttle moves back and forth, continuously passing the weft yarn through the warp yarn. In this method, the weft yarn remains unbroken and connected throughout the weaving process, which is a major advantage. Because there are no cut ends, there is no need for machine stitching on the edge of the umbrella, resulting in a sharp and very refined finish.
Today, Yamanashi Prefecture is the only place where small, narrow-width fabrics are woven with shuttle looms specifically for umbrella material.

A design showcasing the “narrow-width” fabric without machine stitching on the edge, which is a highlight of the “Two Ply” series

How Koshu-ori is Made
In Fujiyoshida, Yamanashi, Koshu-ori is still made through multiple specialized steps—just as in the past. Weavers, dyers, warp preparers, thread setters, and finishers all play a role in bringing this fabric to life. Here, we introduce the traditional process behind Koshu-ori.
How Koshu-ori is MadeJapanese Style Folding Umbrellas
Two Fold Umbrellas
Japanese-made folding umbrellas have often adopted a frame where the ribs fold outward. Komiya Shoten has adhered to this Japanese style two-fold frames for a long time, ever since it was founded. The silhouette is beautiful, and it pairs well with the high-quality Koshu-ori or natural fabrics. We introduce the appeal of these two-fold folding umbrellas.
The Appeal of Two-Fold Folding Umbrellas by Komiya Shoten
Related articles
-
-
"kata kata x Komiya Shoten" -Leaf design on umbrella fabric-
-
A legacy of passion - "Komiya Shoten's Western-style umbrellas" take shape in a turbulent market -
-
Passing on the passion - Meeting with the second president, Takeshi Komiya -
-
Passing on the Passion - Portrait of Founder Takamasa Komiya -
-
"I want to make a beautifully shaped umbrella." -What is the ideal umbrella shape for a craftsman?-
-
A craftsman from Komiya Shoten has been certified as a traditional craftsman for the Tokyo traditional craft "Tokyo Umbrella".
-
"Tokyo Umbrella" designated as a traditional craft of Tokyo
-
Yamanashi Factory Tour - How Koshu Weaving is Made